牧激岳国汉再谈激光加工和PCD 超硬刀具
2022-06-18 13:44:38 阅读次数:4497
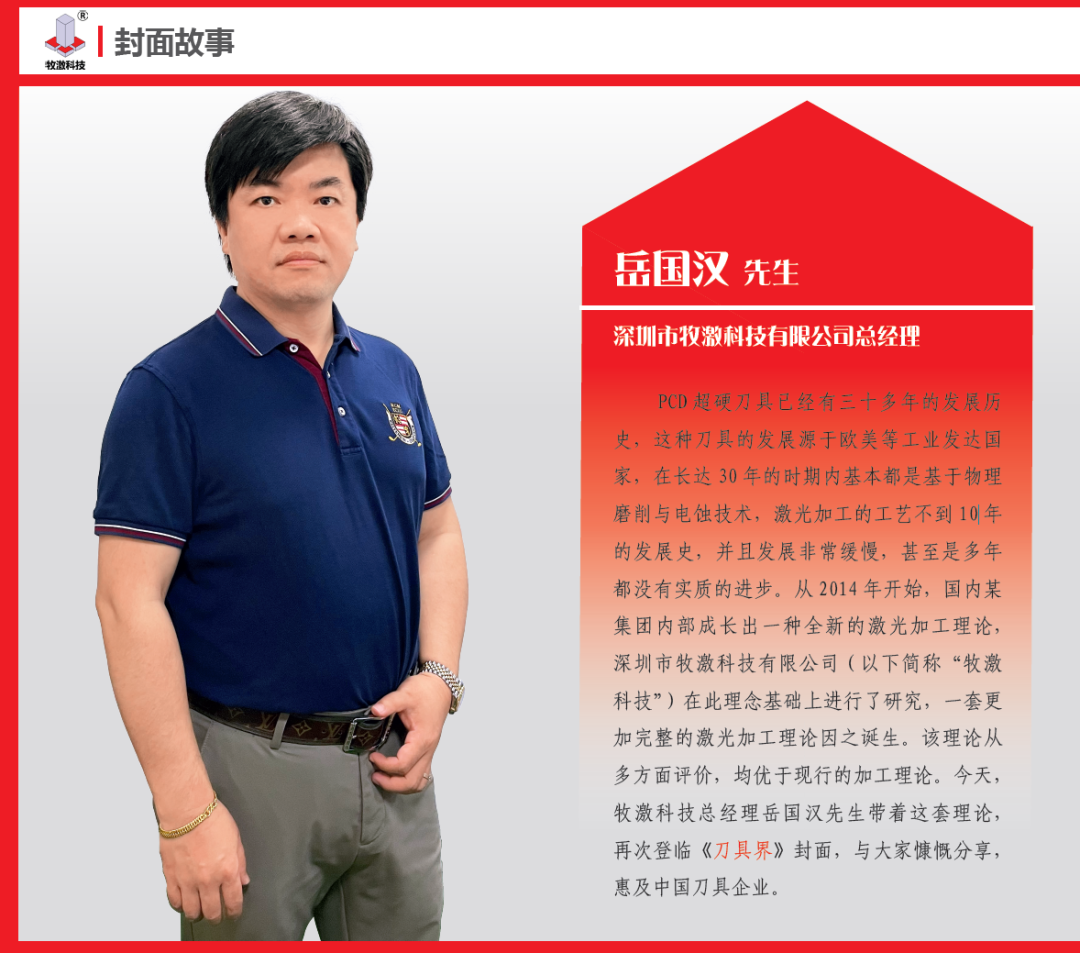
PCD 超硬刀具已经有三十多年的发展历史,这种刀具的发展源于欧美等工业发达国家,在长达30 年的时期内基本都是基于物理磨削与电蚀技术,激光加工的工艺不到10 年的发展史,并且发展非常缓慢,甚至是多年都没有实质的进步。从2014 年开始,国内某集团内部成长出一种全新的激光加工理论,深圳市牧激科技有限公司(以下简称“ 牧激科技”)在此理念基础上进行了研究,一套更加完整的激光加工理论因之诞生。该理论从多方面评价,均优于现行的加工理论。今天,牧激科技总经理岳国汉先生带着这套理论,再次登临《刀具界》封面,与大家慷慨分享,惠及中国刀具企业。
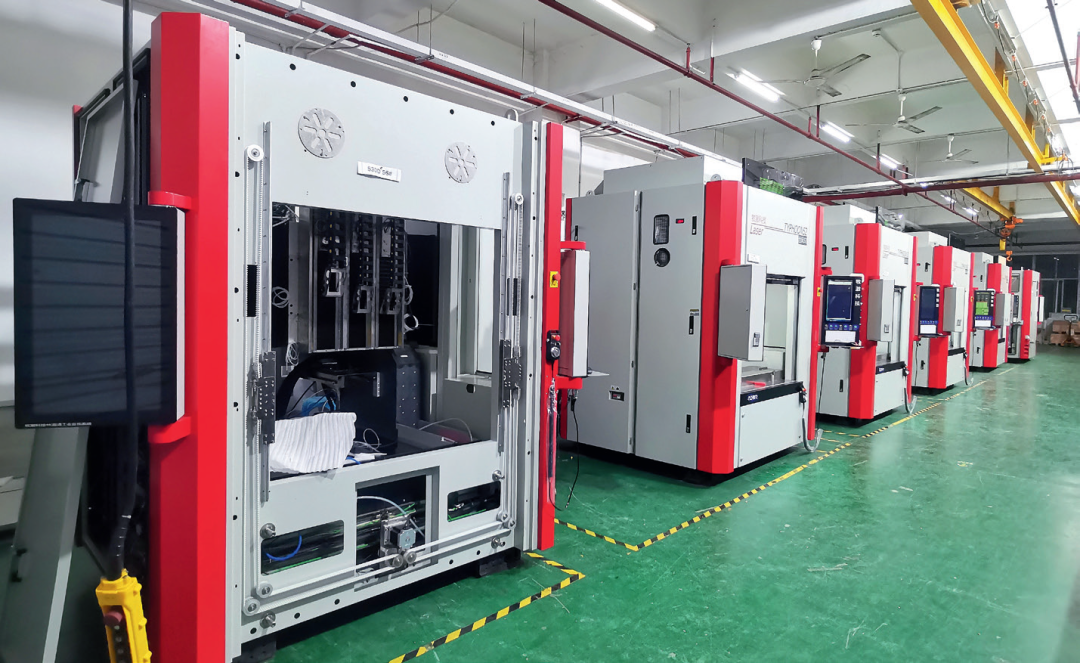
530D 生产现场
牧激科技从PCD 材料的本质出发,推出了基于激光的全激光加工理论。岳总表示,这里要从原材料说起。凡是从事过PCD 刀具加工的人,都知道PCD 的一个主要特性便是它的导电性。而原本PCD 材料并不导电,为了服从加工需求,PCD 材料被改良成为一种类似金属的材料,便于火花机加工。无论是线切割或铜轮放电都是火花机,通过导电电弧的熔化金属结合剂的高温使PCD 碳化, 达到对PCD 的精密加工。放电电流越大,产生的温度也就越高,同样加工效率就变高;温度越高,PCD 碳化就越严重。为了降低刀口的碳化,提高刀具的切削性能,不得不调低电流,降低加工温度, 加工效率直线下降。过去做一把PCD 刀具都是按小时计时,有的甚至多达数天才能完成一把刀具。
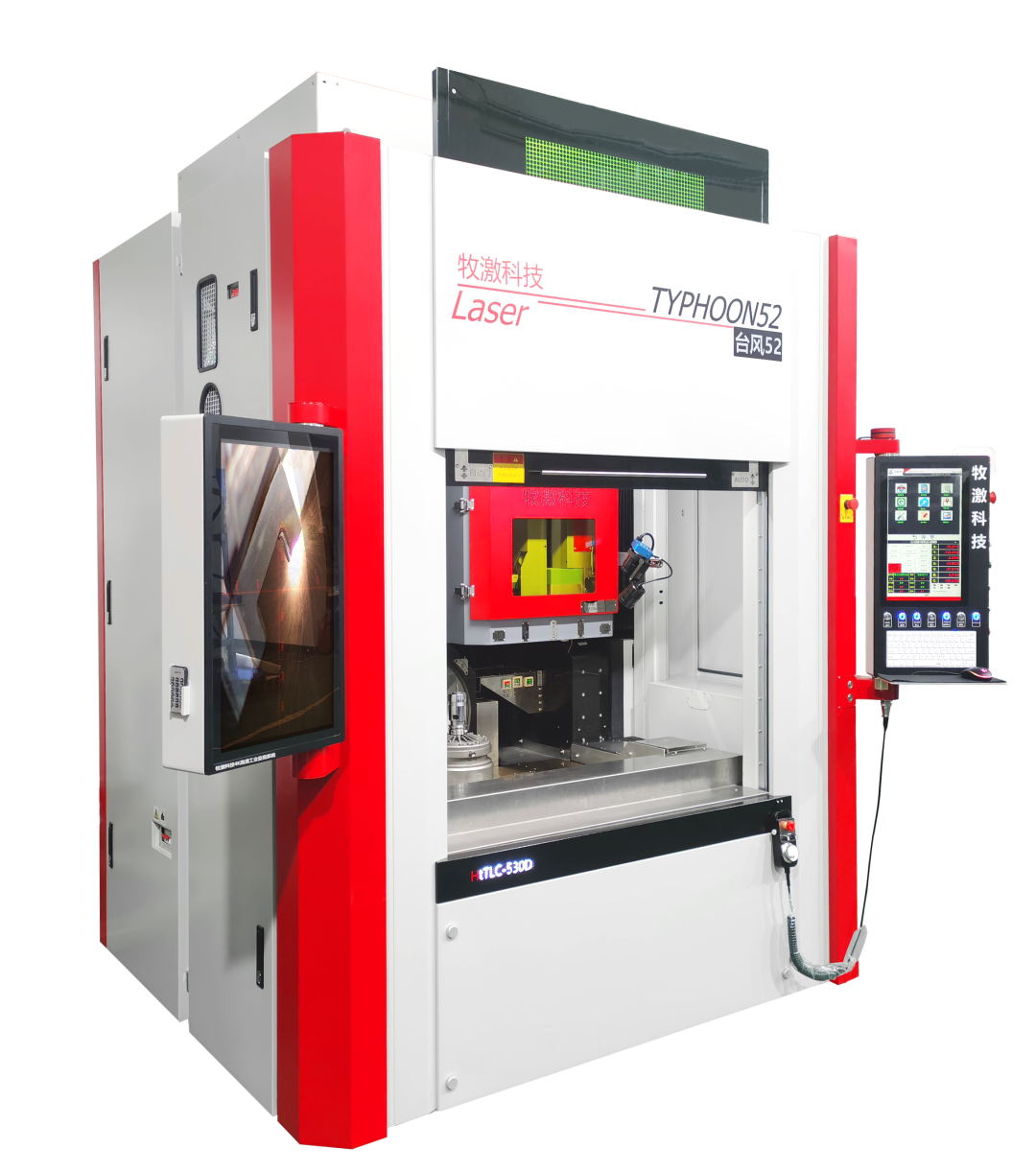
“除了效率低之外,还有刀口崩口和不锋利等问题,约束了PCD 刀具的快速发展。” 岳总说,“再加上在PCD 材料中过多的考虑导电性,导致PCD材料的耐磨性严重降低。各种综合因素加在一起,使PCD 刀具成为了超贵刀具的代表,便宜的几百元一支,贵的几万元都有,整体硬质合金刀具的性能提升和价格一路下调,发展势头压过超硬刀具。而在超硬刀具加工技术方面,欧、美、日一直都没有一个更好的方案,直到2019 年。” 2019 年,牧激科技回归超硬刀具领域,带来了全新的激光加工理论。岳总介绍道:“这套理论的第一条, 就是还原超硬本色。PCD 无须导电, PCD 材料从原料到刀具成品全过程都不接触电,100% 去除电加工的影响。材料压制成功后,第一道工序由激光平面磨床完成。2019 年牧激科技快速完成该技术研究,加工一片55mm 直径的PCD,磨削0.5mm,用时不到10 分钟,显著降低了高性能PCD 材料的磨平成本。” 2019 年,很多企业仍然购买一种非常落后的灯泵激光。其实早在2014 年,牧激科技在富士康内部用光纤激光代替了灯泵激光,一台设备相当于8 台灯泵设备,并且几乎无需维护。2019 年推出了更加先进的光纤切割机, 2021 年推出了轴闭环五轴激光切割机, 更便宜、更高效、更高品质、更强的专业针对性。“焊接是所有PCD 刀具都要面临的问题。激光焊接技术可以精准的实施控温焊接与换片,并且可以在五轴机上实现局部刀片换片,这一技术在大型刀具加工的应用上意义重大,可以实现一次装夹一次校正多次加工,实现精密局部换片。” 岳总说。从PCD 原材料开始, 牧激科技的激光加工都在尽可能的保护材料原始特性,刀具加工上的保护更加关建。这一技术就与欧美存在明显不同,岳总称之为“精粗精工艺”。“精粗精” 分别代表:第一步精密激光加工,第二步大功率激光粗加工,第三步精密激光精加工。为什么要采用这种工艺?完全是从保护刀口出发,充分利用激光加工特性,追求高品质的同时,也要保证高效率。为什么第一步是精加工?这无疑颠覆了大家以往的加工认知。岳总为我们释疑:“ 熟悉PCD 材料的人都知道,PCD 表面是PCD 层,其下是硬质合金的衬底。第一步采用大功率激光粗加工时,PCD 层直接受热非常严重, 而PCD 层中绝大部分都是导热性极佳的金刚石。PCD 层在粗切激光的作用下,热损伤深度可达0.2mm 以上,并且粒度越大,热损伤层越深。” 于是, 加工PCD 层的时候, 牧激科技采用精密激光系统,并且采用超低损伤的加工参数,切割出一条约0.5mm 左右宽的沟槽。一定要切除所有PCD 层, 通常0.6mm 厚的PCD, 两刀便能切除完成。
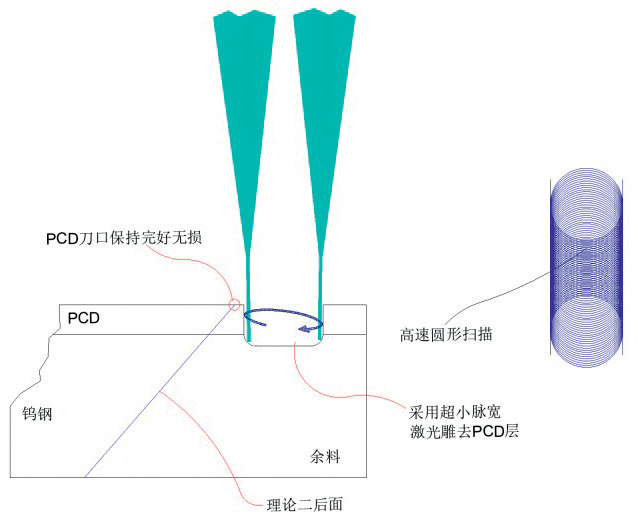
预切理论图片
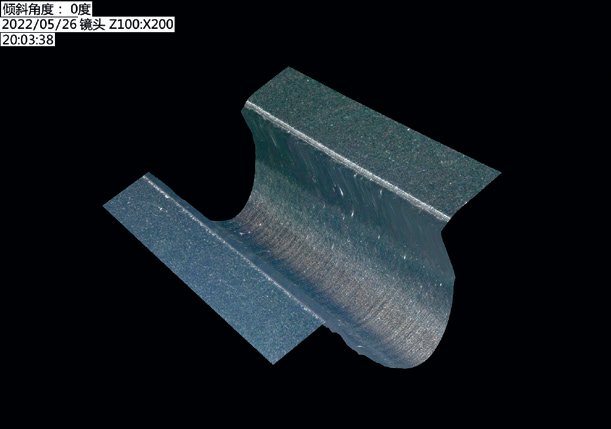
预切沟槽照片,可见刃口没有烧伤
如何切割出一条宽度0.5mm 的沟槽?岳总答道:“我们采用了光刀方法, 让激光高速旋转切割,这种方法是我们2014 年发明的。截止目前,与国外技术已有两处明显的不同。PCD 层切割完成后,采用一套大功率激光,固定式切割头切割PCD 槽内,大功率粗切激光不能切到PCD 层,激光直接将钨钢衬底切除,完成‘精粗精’ 中的第二步。”
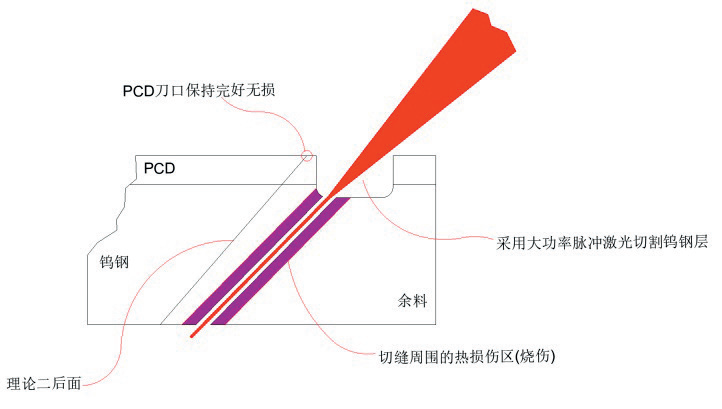
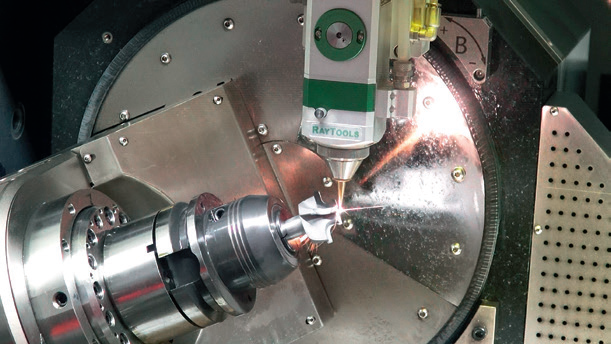
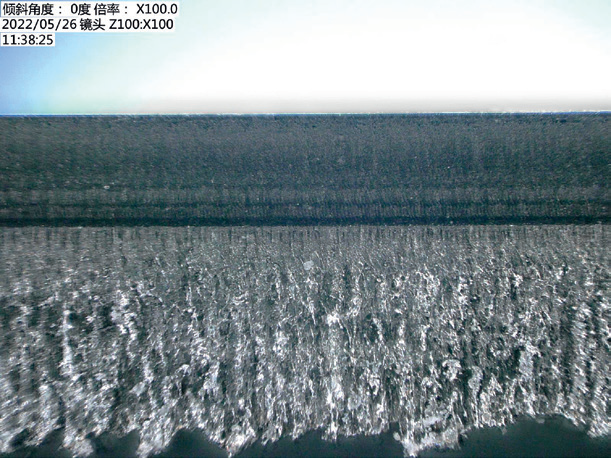
粗切照片,粗切没有切到PCD,
但是粗切的刀面并不光滑
那么,为什么一定要粗切这一刀呢?难道不能采用光刀一直向下切割吗?“这个问题,我们在设计双激光设备的时候专门进行了研究。如果采用光刀一直向下切,的确可以切除多余的材料,时间会比较长。当材料厚度较厚的时候,用光刀向下切割是十分困难的,因为排屑非常困难,并且还会在刀口处留下大量飞溅出来的钨钢颗粒。由于这些钨钢颗粒的温度相当高,并且含有钴,飞溅到PCD 表面后,与PCD 的结合剂熔合,非常牢固的粘在PCD 表面,无法用常规清洁手段清除。而这些留在刀口的异物,会严重影响刀具的切削性能。”
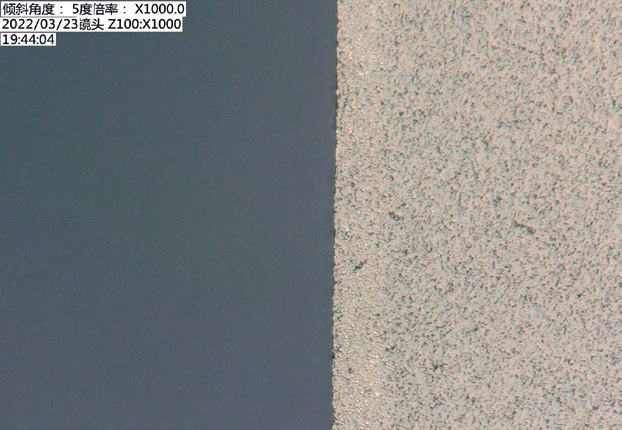
牧激科技创新地将两套激光系统设计在同一台设备中,方便随时快速切换。粗切时角度比设计的后角要大一些,因为切割的面并不光滑,需要再用精切激光对后刀面进行精修,以保证后角的精度与后刀面的光滑度。由于有粗切激光切除掉钨钢衬底, 精切激光加工大后角时,钨钢颗粒全部向下飞出,PCD 表面及刀口没有任何加工造成的异物,排屑顺畅,没有高温钨钢颗粒再熔现象。加工中的刀具温度也相对低了很多,通常加工完成后,可以用手直接摸刀具。同时, 因加工余量减少,精加工后刀面的时间也相对减少约50% 以上。以1.6mm 总厚的PCD 为例,整体加工效率提升约一倍。增加了一套大功率激光系统, 相当于增加了一倍的产出。
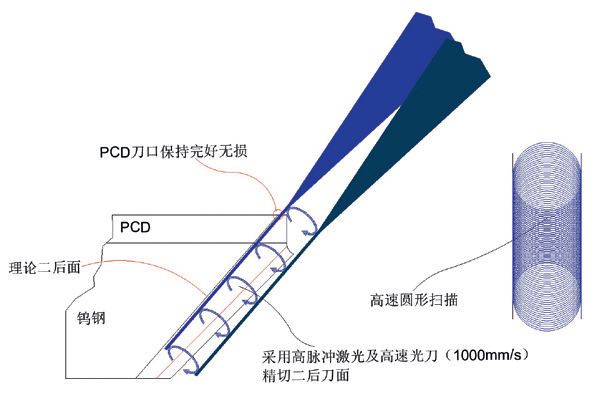
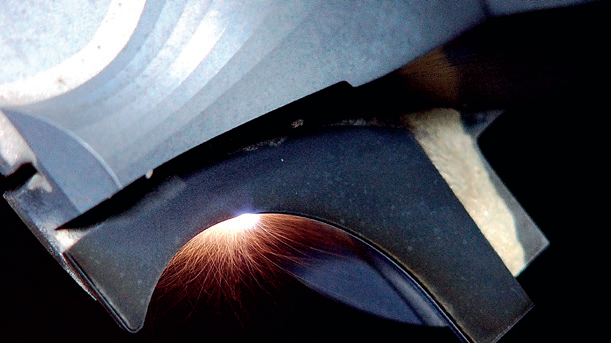
4K 开槽的视频照片
谈到此处,岳总归纳说:” 以上几步都还没有到修刃口。以往,进口设备都不采用激光进行以上加工,而是以线切割配合完成。激光只加工刃口几个丝的余量,甚至要求不高的PCD 刀具,线切割便直接做好,这就是本质的差异。当初我们推出双激光的时候,还有很多人不能理解,认为多加一个粗切,用途并不明显。这种认知, 源于学习进口设备加工方法的惯性思维。而我们却是从加工的本质出发, 研发出科学的方法实现高效生产。” “精粗精” 的第三步就是精修。包括精修大后角、小后角和刀口,这一点也与进口设备完全不同。而这也是令岳总颇为自豪的一点:“因为,这是我发明的反切反修方法。这个方法,2016 年成功完成了某大牌手机的高亮黑铝合金外壳加工,全球只有中国人能做到。如今,我再一次将这种技术进行了升级, 不但能实现当年的功能,还增加了更多有利于提高刀具寿命的方法。”
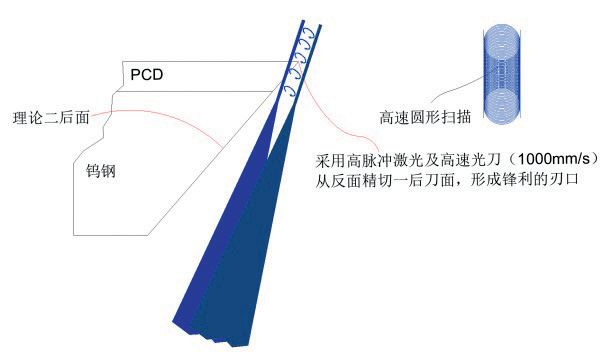
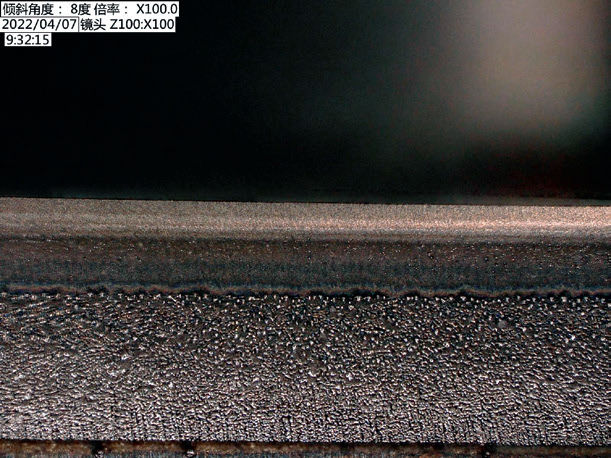
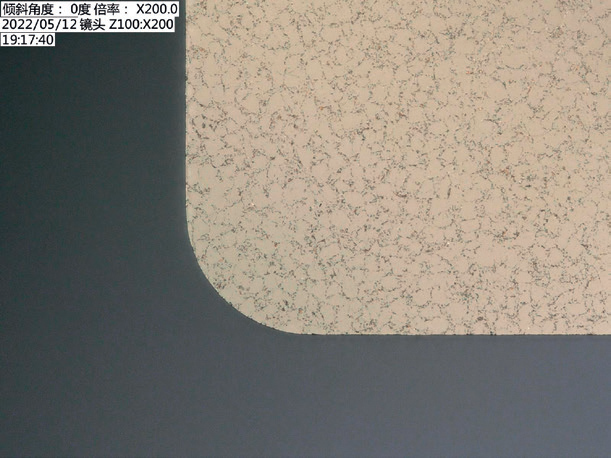
反切刃口的优点有三个:其一, 刀口非常锋利;其二,刀口没有烧伤;其三,第一后刀面非常光滑。对此,岳总特别进行了说明:“国外的公司宣传用皮秒或飞秒激光来减少刃口烧伤,而牧激科技却用纳秒激光就解决了烧伤。不是没有烧伤,而是我们把烧伤留在非刃口的位置。纳秒激光不但比皮秒、飞秒激光更便宜, 加工效率还要高出数倍。”
某品牌正面有黑线照片
与牧激正面没有黑线照片对比
说到这里,岳总回忆初衷:“当年, 我只是因为想提升刀具寿命。当时, 完全不懂PCD 刀具,只想把刀具做得更锋利,却不知太过锋利的刃口,寿命更短。直到2021 年,我才找到原因。” 2020 年, 岳总开始重新投入了PCD 刀具的研发。从理论上说服自己, 用实践数据证实理论,在行业专家的指点下,岳总试着减少第一后角,发现寿命明显改善,进一步研究出钝化后角设计,寿命问题彻底解决,完成了第一版PCD 刀具的新理论。相比欧美先进的刀具技术,牧激科技更加推荐采用锋利刃口设计。锋利刃口更利于切削,同时采用的钝化刃口设计, 满足了锋利与寿命的要求。锋利刃口有效降低了切削阻力,使得PCD 刀具的直径进一步变小,加工的壁厚也可以更小。”
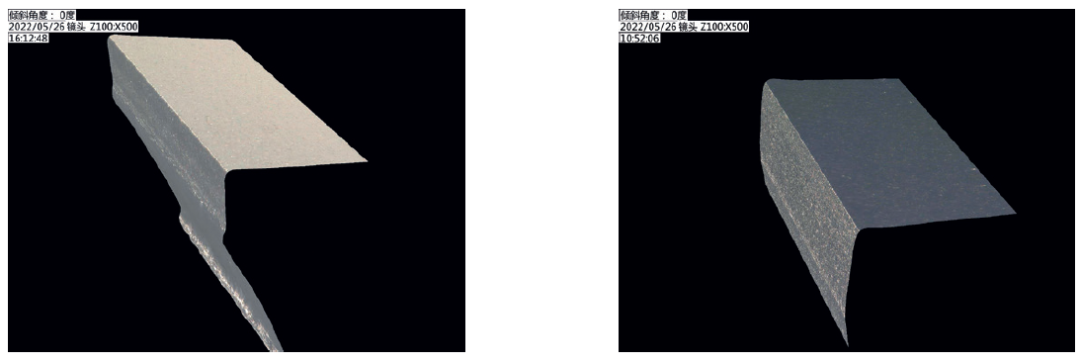
某品牌45 度立体照片
与牧激45 度立体照片对比
现在,我们跟随着岳总,对牧激科技的全新PCD 刀具理论进行一下总结:采用全激光技术,原材料不用导电,耐用性更好;采用“精粗精”加工,最大限度保护了PCD 刃口材料及刃口品质, 实现了高效加工;采用反切刃口技术, 实现了锋利刃口和无烧伤的刃口,加工出锋利却又有钝化功能的刃口,同时提升了刀具的性能与寿命。
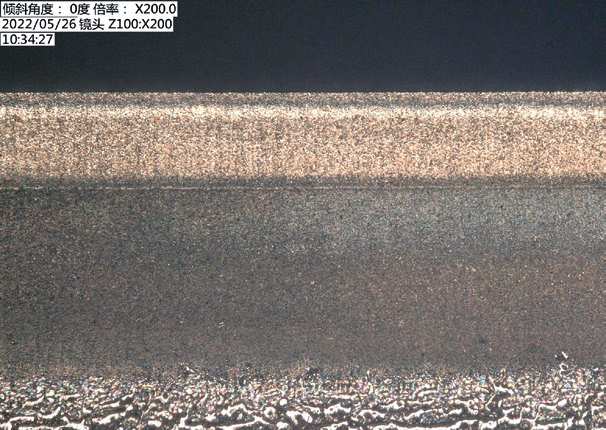
采访最后,岳总自信且坚定地说:“今时今日,在PCD 刀具的加工技术上,牧激科技已经领先一步,加上我们更加认真的超精密设备技术,精度做到了完全不亚于进口设备,效率高出数倍,配合国产专用材料,国产高性能PCD 刀具已成现实。我们不支持内卷,刀具越来越便宜,全部是技术进步的成果。”
